Our Products
Hydraulic cylinders and jacks
Niu Li Tools is one of the leading manufacturers of various hydraulic cylinders and jacks in China. We provide all types of jacking and lifting solutions directly to customers worldwide at factory direct prices and excellent quality. Our hydraulic cylinders can be used for lifting, pushing, pulling, bending or holding applications in most industrial and commercial work environments. Niu Li Tools offers hundreds of hydraulic cylinder configurations in terms of capacity and stroke, ranging from 4 tons to 2000 tons and strokes from 10 mm to 2000 mm.
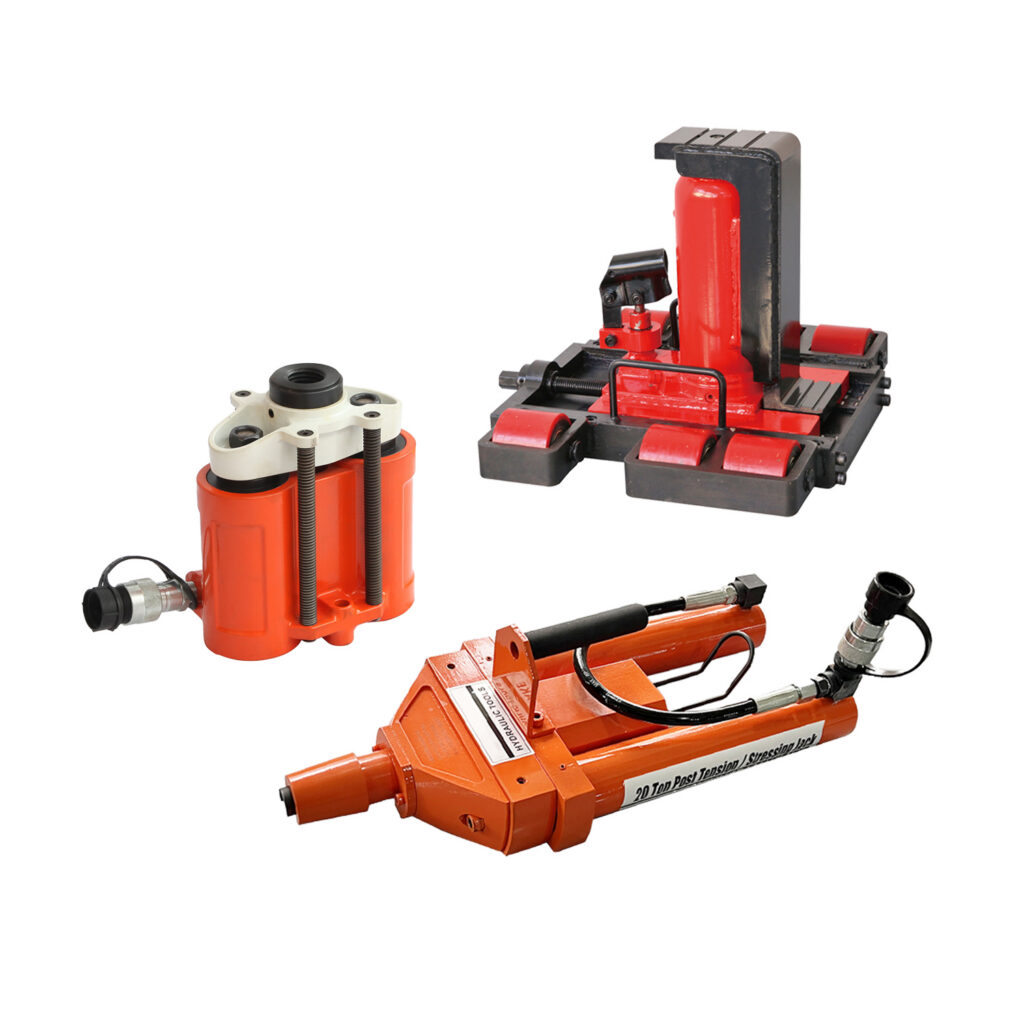
Bolt Tools
Newton Tools offers a wide range of hydraulic torque wrenches, torque multipliers, hydraulic nuts, bolt tensioners and hydraulic power units for a variety of bolting applications.
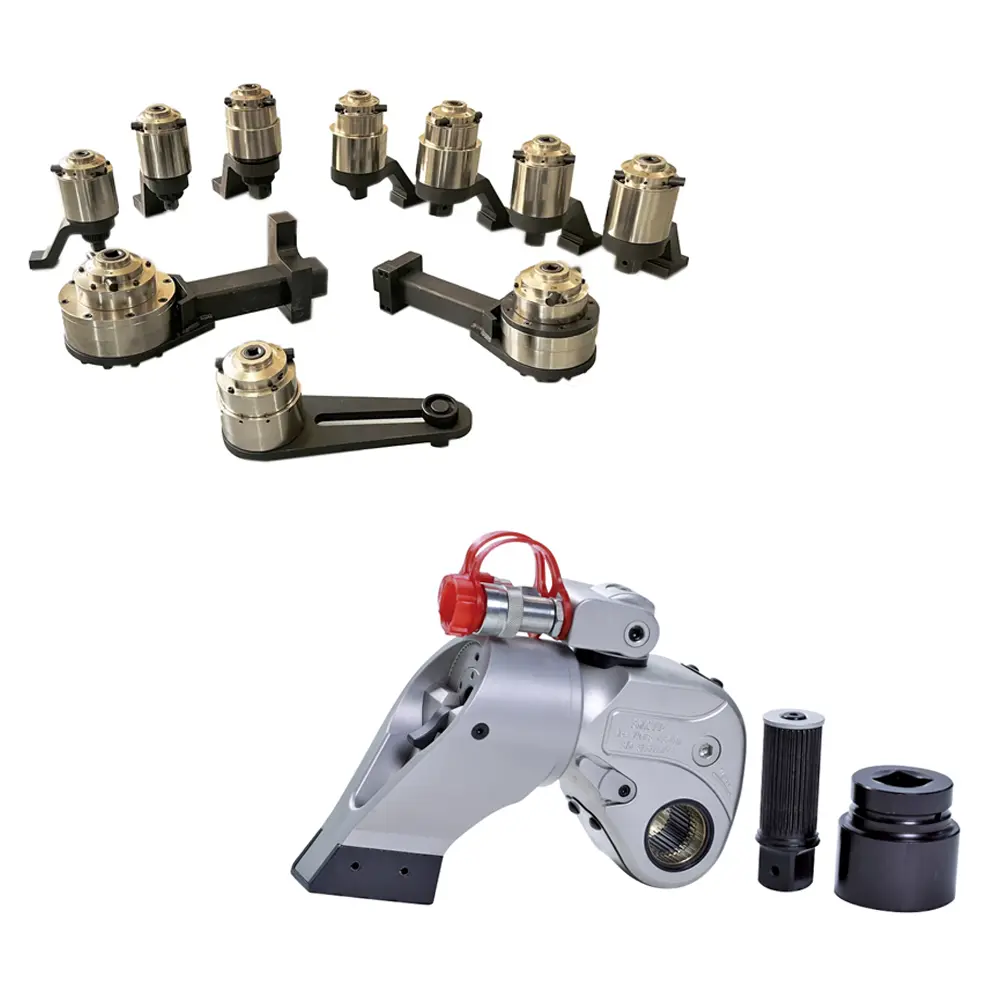
Flange maintenance tools
Comprehensive range of hydraulic and mechanical alignment tools, hydraulic nut splitters, hydraulic flange pullers, and a wide range of mechanical and hydraulic spreading tools for breaking apart stubborn joints.
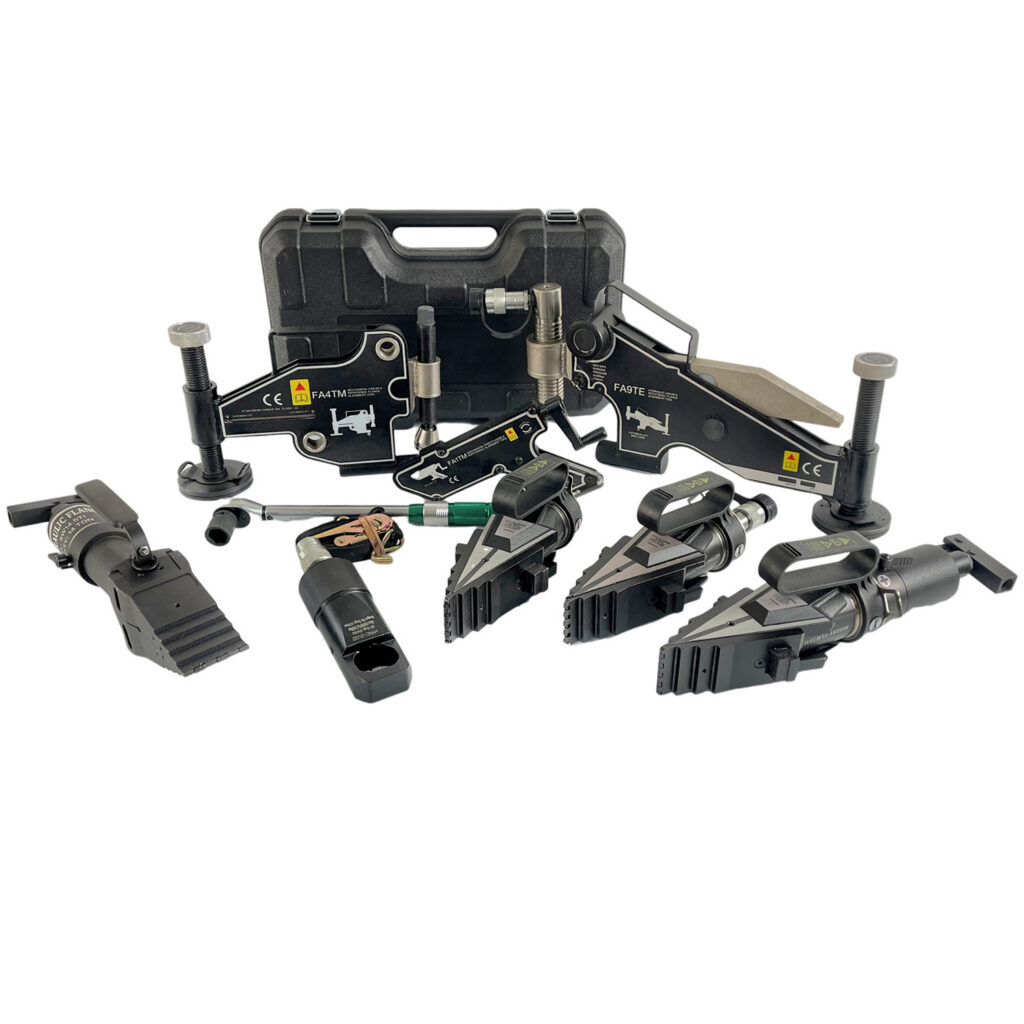
Hydraulic and mechanical pullers
Hydraulic and mechanical pullers are used to remove shaft mounted parts (bearings or couplings). The capacity of hydraulic and mechanical pullers from Newton Tools ranges from 2 tons to 600 tons. In addition to railway vehicle maintenance, machinery installation, mine maintenance, construction support, it can also remove round workpieces such as pulleys, gears, bearings, etc. in various mechanical equipment.
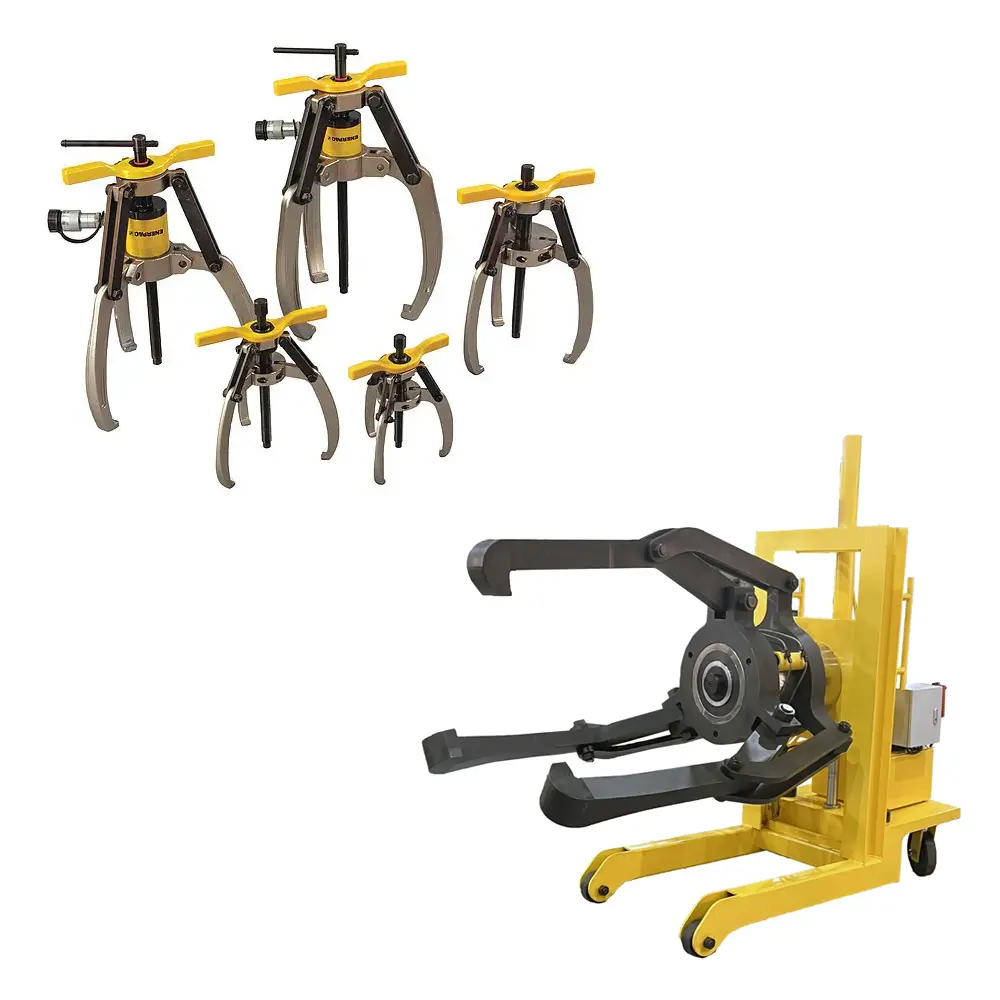
Hydraulic cutters and crimping tools
When you need to cut heavy bars, chains, cables, nuts and similar materials, or if you need to find the right crimping tool, you need look no further than Newton Tools’ wide range of cutters and industrial presses.
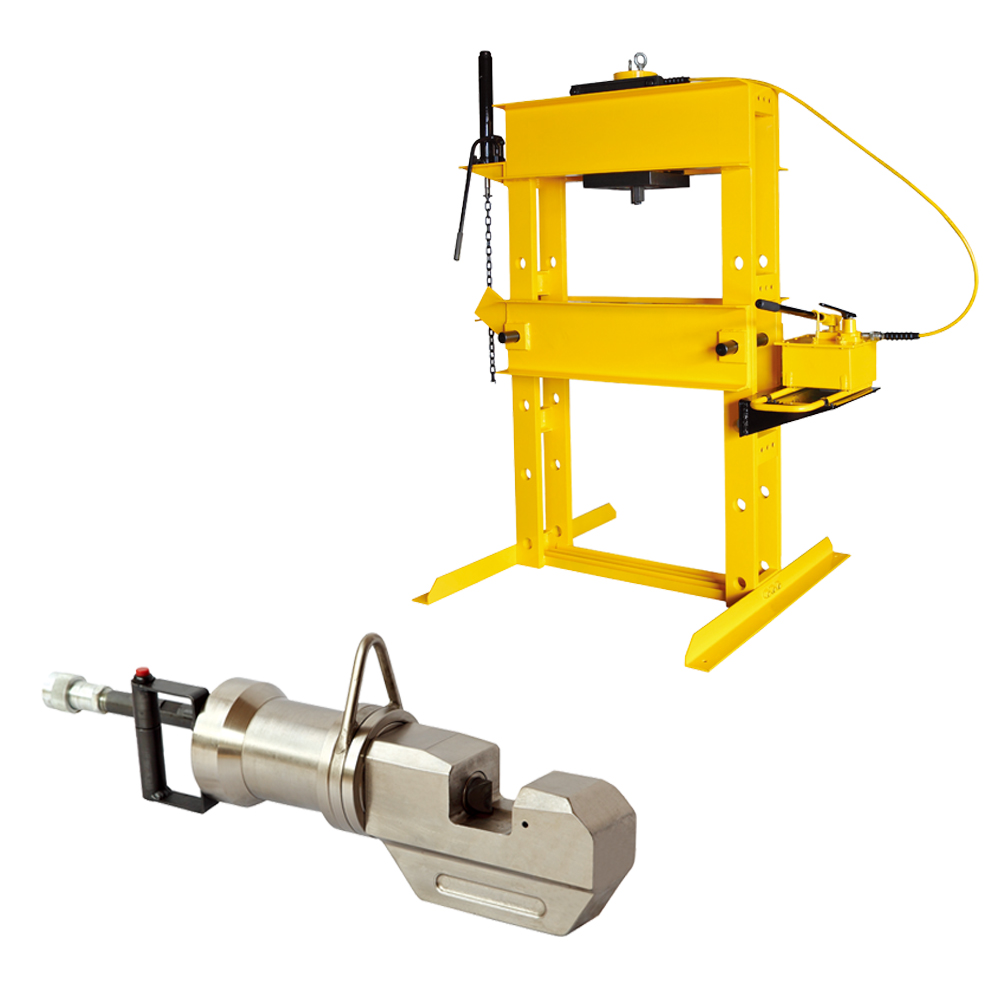
Hydraulic pumps and power units
Newton Tool Hydraulic Power Units are available in a variety of different configurations. Whatever performance, speed, control, intermittent or heavy-duty performance your high pressure pump requires, you can be sure we have the right hydraulic power unit for the application. Available in manual, electric, air and gasoline powered models with multiple reservoir and valve configurations.
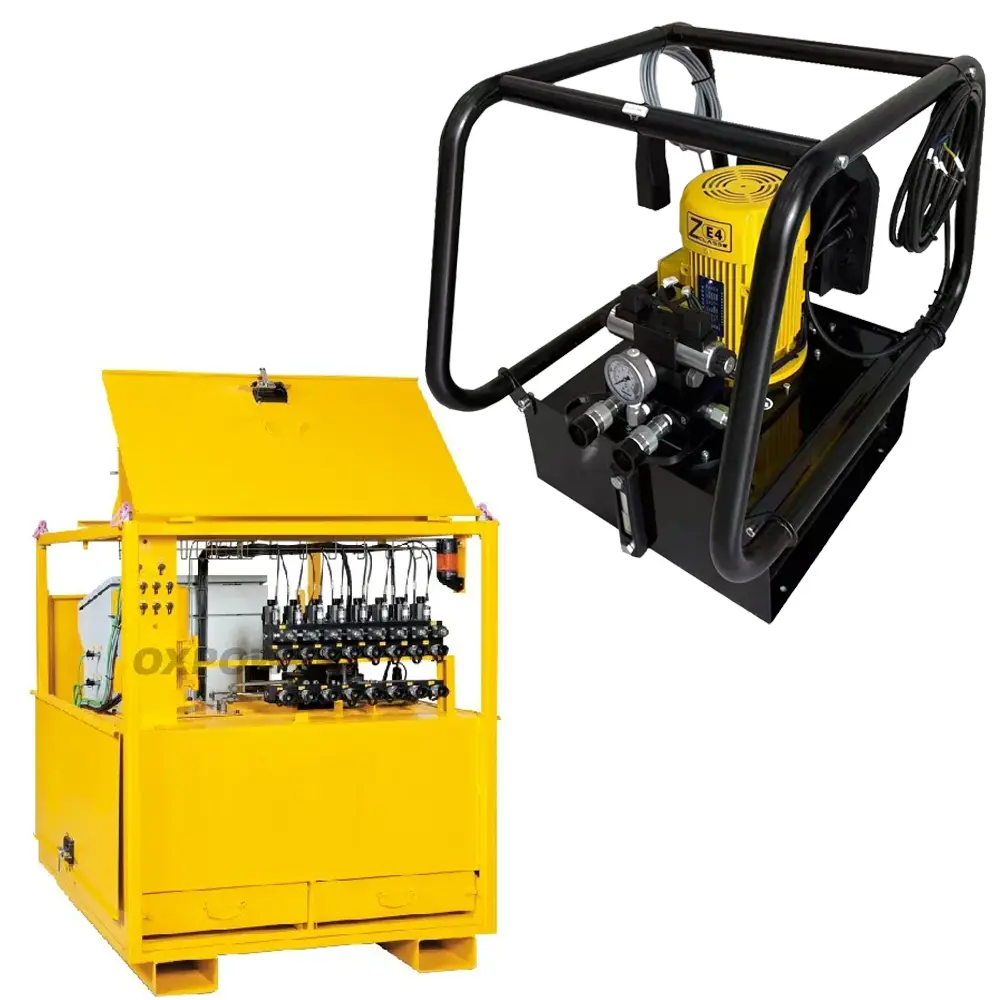
Auto Maintenance Tools
OXPOWER Tools offers a wide range of non-standard bearing repair and automotive maintenance tools in a variety of sizes, capacities and styles. Whether your application requires mechanical or hydraulic, OXPOWER can meet your needs. Made of high-strength alloy steel, the puller can provide years of trouble-free operation even in the harshest environments, and you can rely on it.
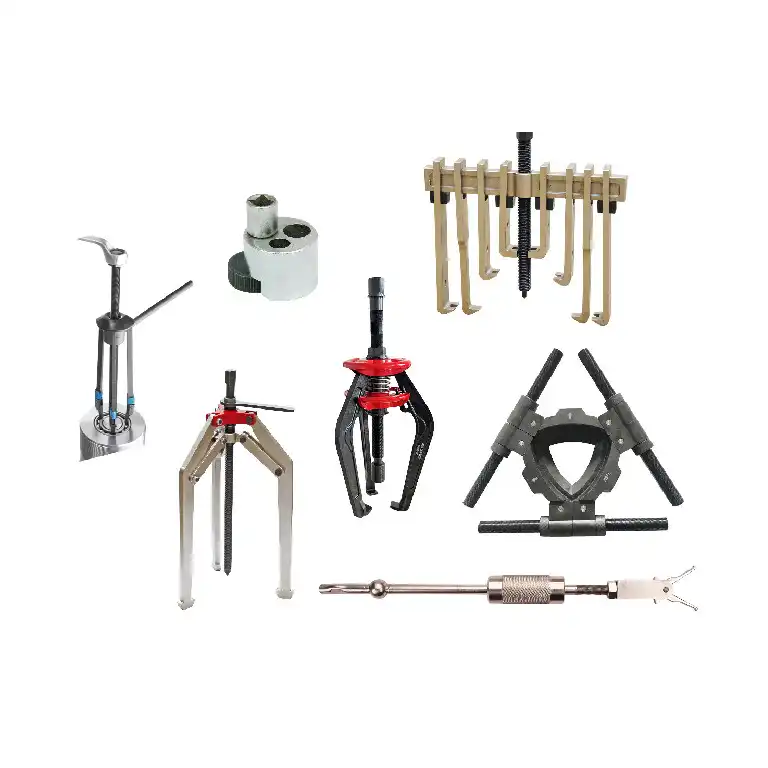
Hydraulic accessories
A line of hydraulic accessories including quick connectors, adapters and distributors, pressure gauges and adapters, fittings and diverter manifolds, safety valves, pressure regulating valves, check valves and flow regulating valves, directional control valves, hoses and pressure sensors for reliable fluid power system integration and performance in all industrial machinery.
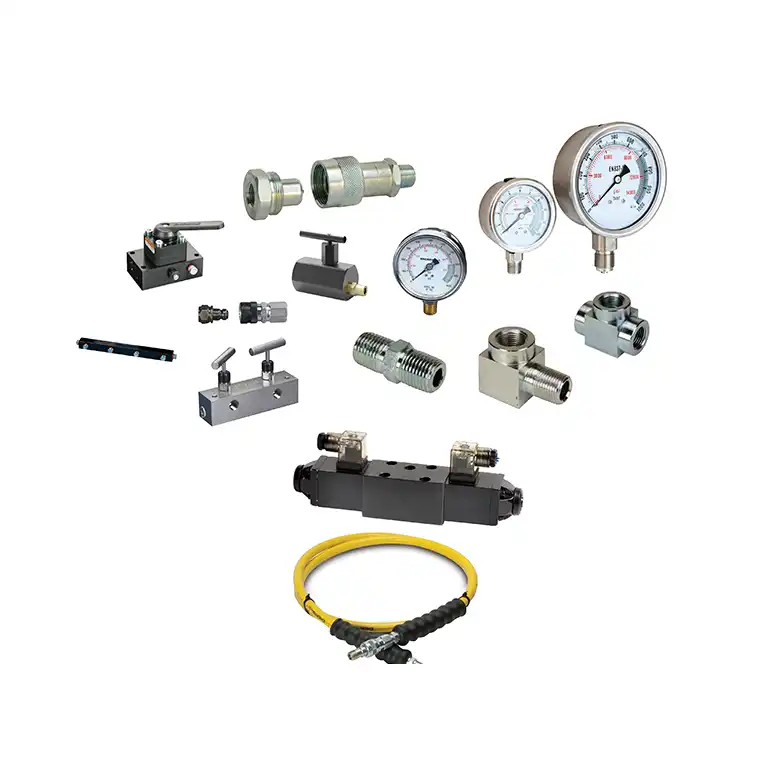
For business use
Widely used in pipeline maintenance, pipeline construction, testing and flange replacement, maintenance gaskets, pressure vessels, cylinder head opening, power plants, bearing removal, oil and power drilling, motor rotor removal, offshore platforms, jacking work, shipbuilding, industrial equipment, horizontal movement of workpieces and other industrial applications.
Latest Articles
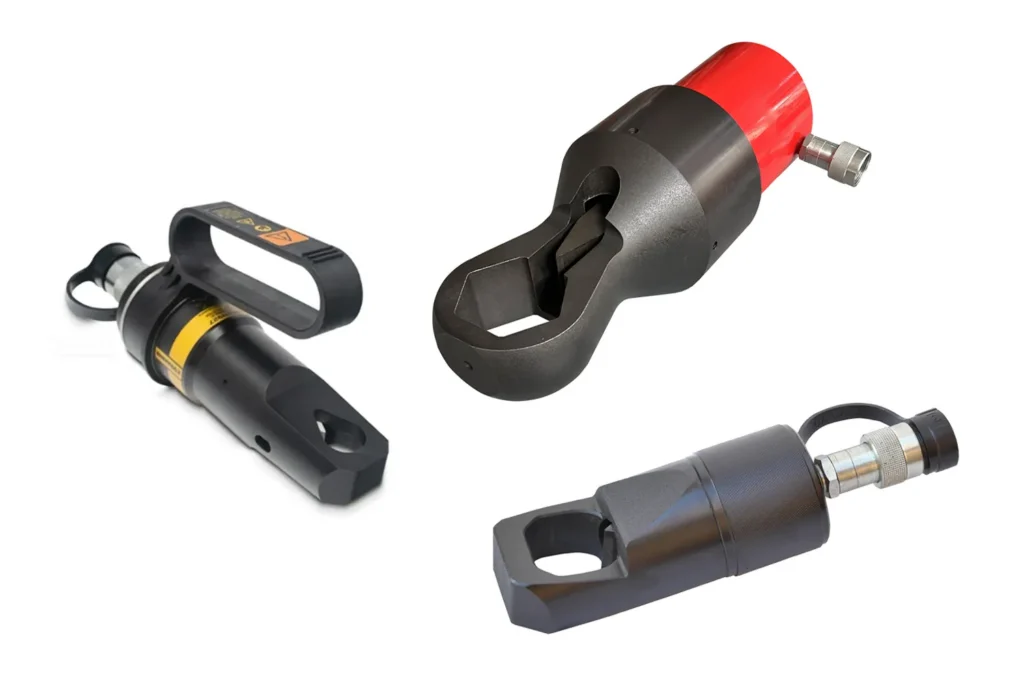
What is a Hydraulic Nut Splitter?
Specialized tools and equipment are essential in industrial maintenance and machinery repair. The hydraulic nut splitter is one such tool that plays a vital role in disassembling and repairing heavy machinery. The purpose of this article is to give readers a comprehensive understanding of hydraulic nut splitters, including their definition, uses, and importance in various fields. Basics of Hydraulic Nut Splitter To remove rusted or over-tightened nuts from bolts and studs, use a hydraulic nut splitter, a sturdy and precisely constructed tool. These nuts are frequently used in high-stress environments such as bridges, pipelines, factories, and large machinery. Traditional methods of nut removal, such as wrenches or torches, can be time-consuming and risky. Hydraulic nut splitters offer a safer and more efficient alternative. How do hydraulic nut splitters work? Hydraulic nut splitters and their cousins Hydraulic nut splitters operate on hydraulic pressure. They consist of a hydraulic pump, a high-pressure hose, and a cutting head. The pump generates tremendous hydraulic pressure, which is transmitted through the hose to the cutting head. The cutting head, equipped with a hardened steel blade, is positioned over the nut to be removed. When activated, the hydraulic pressure forces the edge to close on the nut, resulting in a clean, precise cut. This fast, efficient process minimizes damage to the bolt or stud. Advantages of Using a Hydraulic Nut Splitter Precision and Safety: Hydraulic nut splitters offer precision that cannot be matched by traditional methods. This precision ensures that the bolt or stud remains intact and undamaged during the nut removal process. Time Efficiency: The speed at which hydraulic nut splitters work significantly reduces downtime during maintenance or repair operations. In industries where maintaining machinery uptime is critical, maintaining machinery uptime can result in significant cost savings. Versatility: Hydraulic nut splitters are versatile tools that are capable of removing nuts of various sizes and materials. They are suitable for nuts made of steel, stainless steel, aluminum, and other materials, making them an indispensable tool across several industries. Reduced Physical Stress: Operating a hydraulic nut splitter requires less physical effort than a manual wrench. As a result, worker fatigue may be reduced and the workplace will be safer. In summary, hydraulic nut splitters are indispensable in a variety of industries, providing precise, efficient, and safe results when removing nuts from bolts and studs. Their applications are varied, from construction to aerospace, and choosing the right tool is essential to achieve optimal performance. As the demands placed on machinery across industries continue to increase, hydraulic nut splitters are playing an increasing role in maintenance and repair operations, ensuring the longevity and reliability of critical infrastructure and equipment.
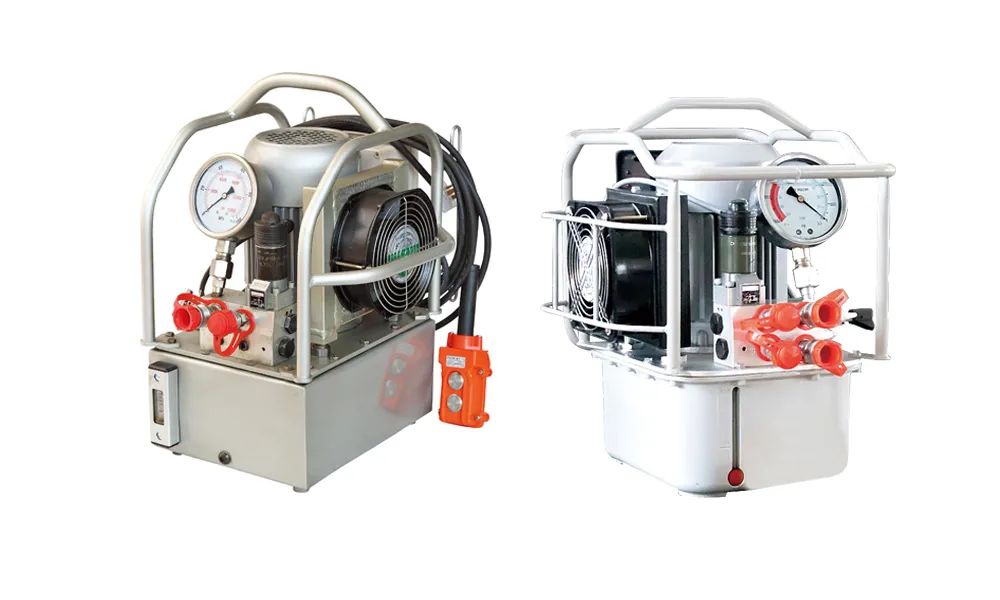
Features of Electric Torque Wrench Pump
In today's fast-paced industrial environment, achieving precise and reliable bolt tightening is essential to guarantee the reliability and safety of buildings and machinery. Traditional manual bolting techniques can provide uneven torque application, leading to equipment failure and safety risks. Electric hydraulic torque wrench pumps have emerged as a reliable and effective solution to these problems. This electric hydraulic torque wrench pump provides reliable power for precise torque application in a compact, efficient design. Hydraulic Torque Wrench System A small, transportable device called an electric hydraulic torque wrench pump is used to power hydraulic torque wrenches in commercial bolting jobs. A hydraulic pump with an electric motor is responsible for providing controlled hydraulic pressure to the torque wrench. The torque wrench then rotates as the nuts and bolts are precisely tightened using high-pressure hydraulic oil. Monitoring Torque Pressure The torque wrench is powered by a high-pressure hydraulic oil hydraulic pump with an efficient three-stage flow pressure design. It guarantees a steady flow of hydraulic pressure for precise and consistent torque application. Users can set and maintain a specified torque value using the torque wrench pump's built-in pressure control system. This feature ensures controlled tightening and prevents overtorque, reducing the risk of component damage. Many modern electric hydraulic torque wrench pumps come with a user-friendly digital display that enables the operator to monitor pressure, torque values, and other important parameters. Motorized Hydraulic Torque Wrench The electric hydraulic torque wrench pump provides unmatched bolt tightening accuracy. It enables the user to consistently achieve precise torque levels, guaranteeing uniform bolt tension across all fasteners. Compared to manual bolting, the electric hydraulic pump significantly reduces the time required to apply torque. Automated operation and quick setup save critical time during the bolting process. Pressure control systems and digital pump monitoring reduce the risk of damaging bolts, nuts, or equipment, preventing over-torque. Ensure Product Integrity The pump tightens large bolts in heavy equipment in steel buildings, bridges, and construction projects. The assembly of components in industrial processes depends on pumps, where precise and consistent torque is critical to product integrity. Ensure proper assembly of wellheads, pipelines, and other important components in the oil and gas sector. Turbines, generators, and other power generation machinery use electric hydraulic pumps for maintenance and care. Improve Industrial Bolting Efficiency The electric hydraulic torque wrench pump is revolutionary in industrial bolting. The technology has evolved to the point where it has become an essential tool in many different industries. It provides precise torque application, time savings, improved safety, and portability. As technology develops, we can expect more improvements in electric hydraulic pumps, bolting process optimization, and overall industrial efficiency.
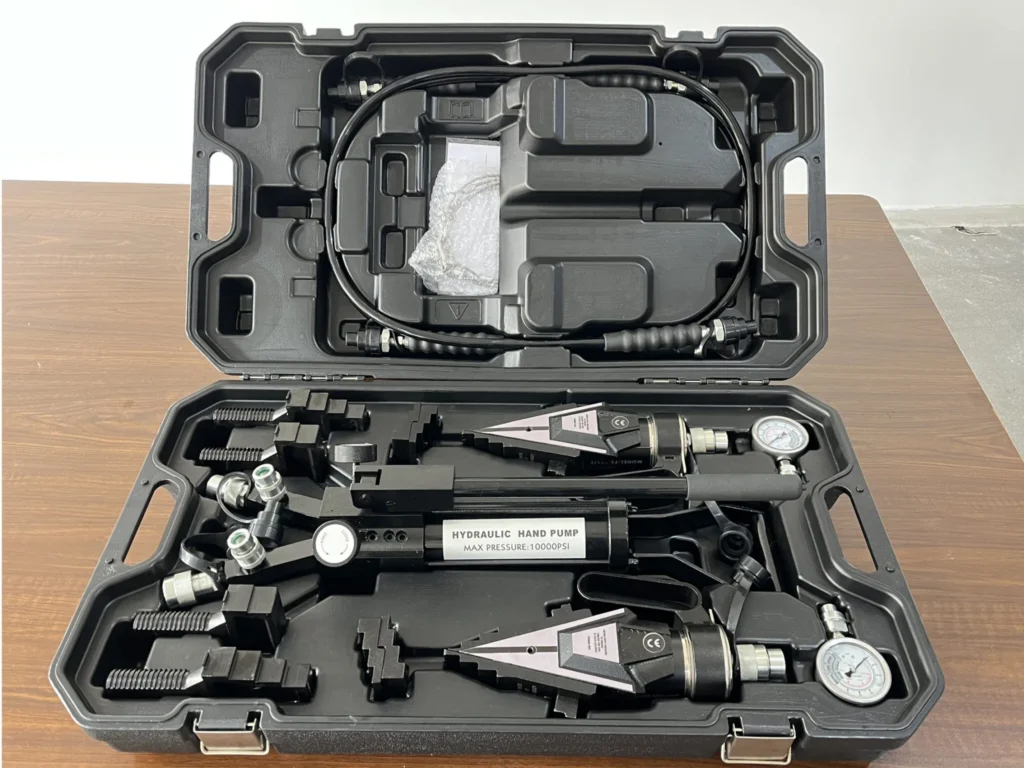
What is a reliable flange separator?
The 24 ton hydraulic flange spreader is a heavy-duty industrial equipment that can handle the toughest flange separation jobs. Heavy-duty applications such as large pipelines, pressure vessels and machinery repairs can benefit greatly from its tremendous strength and force. With a load capacity of 24 tons, this hydraulic spreader can apply tremendous pressure to effectively separate flanges, saving the operator time and energy. Its rugged design guarantees longevity and reliability in difficult working environments. Rugged flange spreaders are essential for safe and efficient flange separation in the oil and gas, petrochemical and various manufacturing industries. High-capacity solution for effective and efficient flange separation The hydraulic flange spreader provides a high-capacity solution for industrial activities that require strong force to effectively separate flanges. It outperforms traditional methods, providing greater efficiency and reducing downtime when performing maintenance or repair work. The spreader can use hydraulic power to apply force accurately and evenly, protecting flanges and ensuring smooth operation. Because it uses a forged high-strength wedge-shaped housing, it is recommended for large projects where efficiency and safety are critical. Capability to carry huge loads. With a spreader range of 6-103.5mm, this hydraulic spreader optimizes performance and simplifies procedures across various industrial sectors thanks to its large capacity and user-friendly features. With its unmatched efficiency, this hydraulic flange spreader revolutionizes flange separation. Conventional techniques can require a lot of time and labor, but this hydraulic spreader speeds up the process with its powerful force transmission. Hydraulic pressure is evenly distributed across the flange, minimizing the possibility of vibrations and erratic movements that can cause accidents. Efficiency leads to reduced costs and increased productivity, thus elevating the spreader to the status of an invaluable tool for industrial operations. This hydraulic tool guarantees fast and accurate flange separation every time, whether managing scheduled maintenance or handling emergency shutdowns. Integrated safety features The spreader's non-slip surface and ergonomic handle improve operator control and reduce the risk of accidents during operation. In addition, its solid base and reliable locking mechanism guarantee a safe posture. This hydraulic spreader inspires trust in industry experts, allowing them to work efficiently and safely with peace of mind. Safety is a priority at every stage of development. Superior Industrial Spreader This Hydraulic Flange Spreader is considered the top choice in industrial spreaders and stands out for its superior functionality and performance. Its reputation as a trustworthy and powerful tool has led to it being sought after by professionals in various industries. This hydraulic spreader has become the machine of choice for flange separation and related activities in a variety of environments, including shipyards, refineries, power plants and construction sites. Its real-world application record and satisfied users confirm its position as the first choice to overcome the most challenging industrial difficulties.
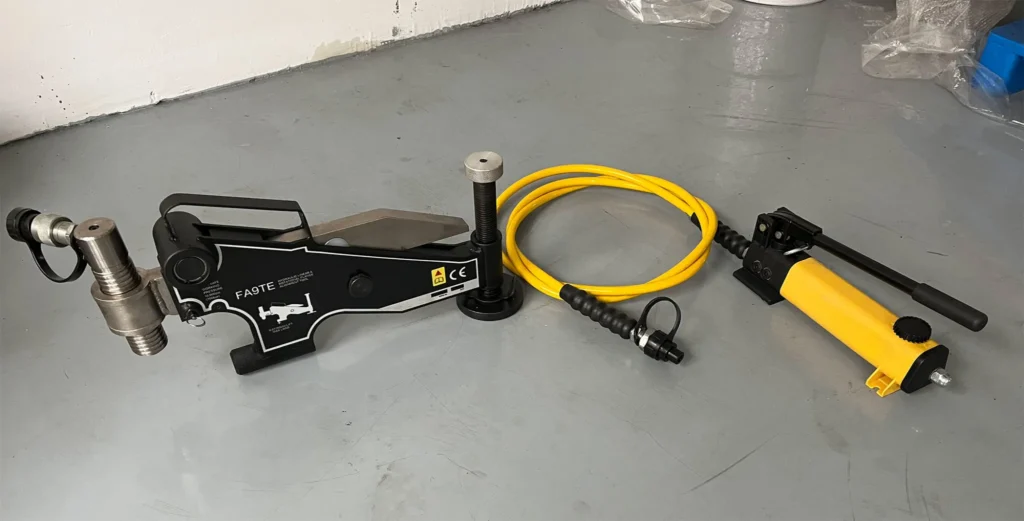
How to use the flange alignment tool?
Flange alignment tools are essential for ensuring that flanges are properly aligned before they are bolted together. These tools come in a variety of shapes and sizes, but most commonly, they feature two or more magnets that attach to the flange faces. The tool then provides a visual indicator of the relative position of each flange face, allowing the operator to make adjustments as needed. Tool Selection Considerations When selecting a flange alignment tool, several factors must be considered. The first consideration is the size of the tool. It should be able to fit the flanges that need to be aligned without being too small or too large. The second consideration is the durability of the tool. It should be made of quality materials and designed to withstand frequent use. Another important factor when selecting a flange alignment tool is its ease of use. It should be easy to operate, even for someone with limited experience using such tools. Additionally, the accuracy of the tool's measurements is essential to ensuring accurate alignment of the flanges. Using a flange alignment tool requires proper technique and safety precautions. The operator must ensure that all bolts are properly tightened before removing any clamps or shims used in the alignment process. Additionally, hands and clothing must be kept away from moving parts during operation to prevent accidents or injuries. Ultimately, choosing the right flange alignment tool will help ensure safe and efficient operations while minimizing downtime caused by equipment failure due to misalignment or misalignment errors. Potential Problems with Misalignment Misalignment is a common problem in flange connections and can lead to major problems such as leaks, equipment failures, and safety hazards. In most cases, misalignment is caused by improper installation or maintenance practices. One way to address this problem is to use a flange alignment tool. This device helps ensure that the two mating flanges are properly aligned before tightening the bolts. To properly use the flange alignment tool, first clean both flanges and remove any debris or rust from the area where the gasket will be. Place the tool on one of the flanges and adjust it until it is flush with the surface. Next, rotate it 180 degrees and repeat on the other side of the same flange. Then continue to align the second mating part of the connection using similar steps. Using an alignment tool will significantly reduce misalignment issues when connecting two pipes together, but there are still some potential challenges to consider when implementing this method in practice. One challenge is to ensure that you have secured both ends of the pipe so that they do not move during the inspection process; otherwise, introducing additional stress points into the system may cause more harm than good. Another challenge can be finding the right tool for larger diameter applications or working in limited workspace areas, which requires specially designed equipment to effectively handle these situations while maintaining the level of precision required for precise alignment results during installation. Conclusion: Properly Aligned Flanges In summary, keeping flanges properly aligned is critical to achieving optimal equipment performance and safety. By following these simple steps when using flange alignment tools, you can help prevent leaks and other problems caused by misalignment or loose connections between pipes or other equipment parts. You can choose from our 4 types of flange alignment tools to handle the above situations, they are FA1TM, FA4TM, FA9TE, FA9TM.
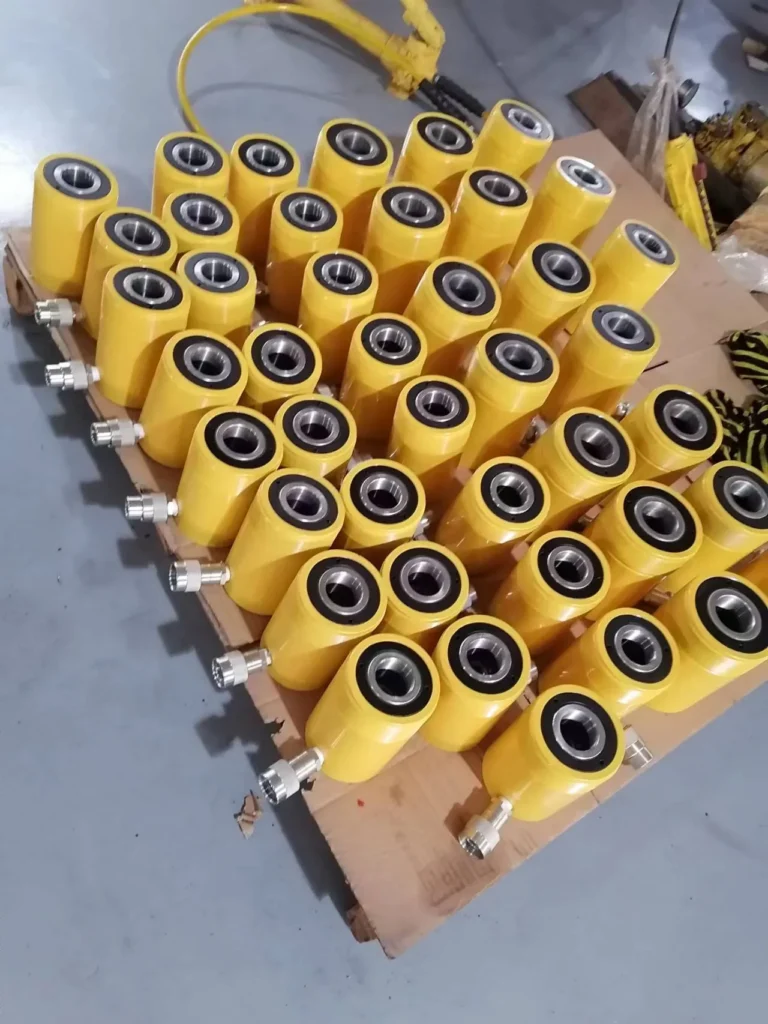
How to fix a leaking hydraulic cylinder?
Leaking hydraulic cylinders can be a nuisance for the average homeowner or professional. If left unchecked, they can lead to decreased efficiency, increased maintenance costs, and even serious system damage. Fortunately, repairing a leaking hydraulic cylinder is usually a simple process if you have the right tools and knowledge. This article will provide a comprehensive guide on how to identify the source of the leak, the materials needed, and how to properly repair a hydraulic cylinder. Safety Measures First and foremost, before attempting to repair a leaking hydraulic cylinder, it is important to make sure you follow all necessary safety measures. This includes wearing protective gear such as gloves and goggles, making sure the machine is shut down and disconnected from the power source, and releasing any pressure from the system. Identifying the Source of the Leak The first step in repairing a leaking hydraulic cylinder is to determine the source of the problem. The leak may be caused by a damaged seal, which can be identified by oil residue around the seal area. If this is the case, the seal will usually need to be replaced. Another potential cause of a leak is a damaged piston rod or cylinder barrel. A visual inspection can help identify any scratches or dents that could cause a leak. It is important to note that identifying the source of a leak may not always be simple. Some leaks are caused by multiple problems at the same time, and some troubleshooting may be required to determine what needs to be fixed. In these cases, a professional with experience in hydraulic systems may need to step in and diagnose and repair the problem. Overall, identifying and repairing the source of the leak is an important part of repairing a leaking hydraulic cylinder. By addressing this issue promptly and accurately, you can avoid further damage to your machine and ensure that it continues to run smoothly for years to come. Removing the Cylinder Removing the cylinder from your hydraulic system can be a daunting task, but it is necessary if you want to repair a leaking cylinder. Before removing the cylinder, make sure you have all the necessary tools and equipment. You will need wrenches, pliers, a socket set, and possibly a crane if the cylinder is too heavy to lift manually. The first step in removing the cylinder is to locate it in the hydraulic system. Once you have found it, close all valves going in and out of the cylinder. This will prevent any fluid from leaking out while you remove the hoses or fittings. Next, use a wrench or pliers to disconnect any hoses or fittings connected to the cylinder. Be sure to place a container underneath the hoses to catch any remaining fluid that may have come out during the disconnection. Once all hoses are disconnected, use a socket wrench or spanner to remove all of the bolts that hold the cylinder in place. Once all of the bolts have been removed, carefully lift the cylinder from its position in the hydraulic system and remove it. Be sure not to damage any surrounding components when doing this. Now that you have removed the leaking hydraulic cylinder from your system, it is time to perform the repair! Cleaning and Replacing Parts A common cause of hydraulic cylinder leaks is damaged or worn seals. To fix this, you must thoroughly clean the affected components and remove the damaged seals. After removing the damaged seal, also inspect the piston rod for signs of damage or wear. Once you have verified that the piston rod is not damaged, replace it with a new one. Before installation, ensure that all surfaces are free of dust or debris, otherwise it may further damage your equipment. After ensuring that everything is clean and in good condition, use an O-ring tool to carefully install the new seal into the groove of the cylinder. Apply some lubricant to both sides of the seal before reinstalling it into its original position. Once completed, test your equipment to confirm if there is still a leak. Repeat these steps if necessary until you have successfully completed the repair job. Reinstalling the Cylinder First, start by removing the hydraulic cylinder from the equipment. Once removed, clean the cylinder and inspect it for any visible damage or wear. If there is severe damage or wear, the entire cylinder may need to be replaced. However, if the damage is minor, you can reinstall the cylinder with new seals to fix the leak. Before reinstalling, make sure to lubricate all O-rings and seals with a compatible lubricant to ensure a proper seal and prevent future leaks. Make sure all bolts are properly tightened to avoid further leaks. When installing new seals or O-rings, make sure to install them in the correct position and orientation as specified by the manufacturer. Improper installation can cause premature seal failure, which can lead to further leaks. Overall, reinstalling a hydraulic cylinder requires patience and attention to detail. It is important not to rush the process, as small mistakes can lead to big problems in the future. Conclusion: Maintenance Tips In conclusion, regular maintenance is essential to keep your hydraulic cylinder in top condition. An important tip for maintaining your hydraulic system is to check and change the hydraulic fluid regularly. …
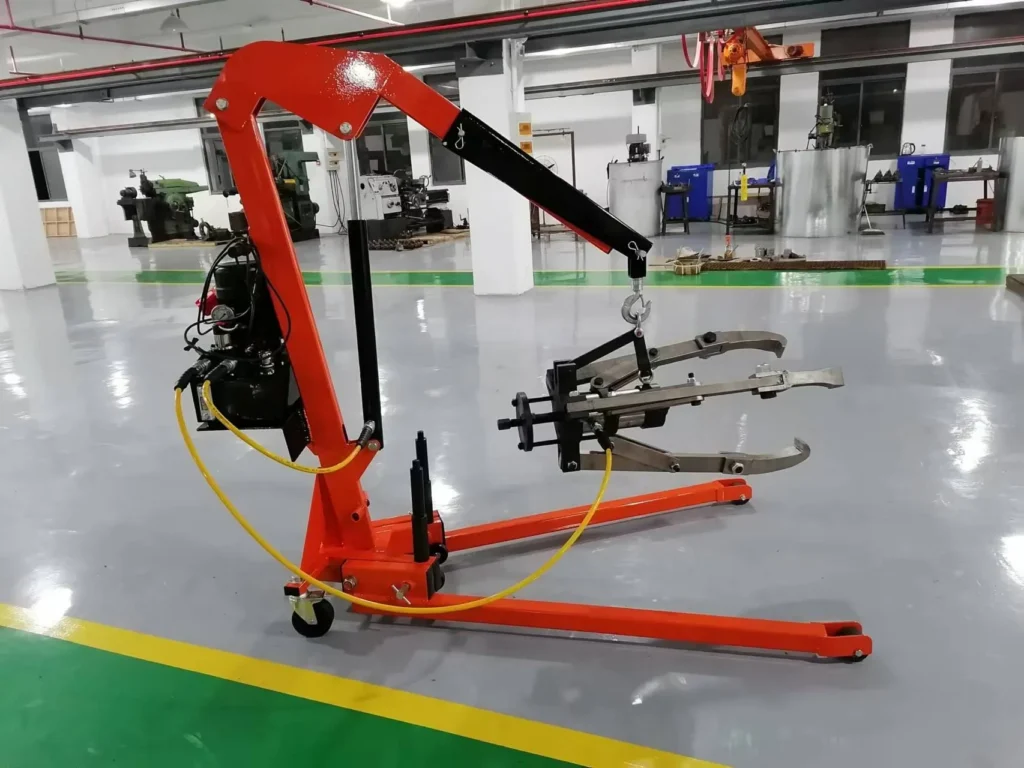
How to choose a reliable hydraulic puller
When working on complex machinery, it is important to have the right tools. Hydraulic pullers are important tools for loosening and removing components in many industrial systems. Choosing the right hydraulic puller can save time and money while ensuring safe operation. This article provides a clear guide to choosing a reliable hydraulic puller that meets all your requirements. What is a hydraulic puller? A hydraulic puller is a machine tool used to separate press-fit parts. It works by generating a strong pulling force to remove the component from the shaft or housing. The hydraulic system has smooth pressure, ensuring precision and safety in operation. Types of hydraulic pullers There are four main types of hydraulic pullers: claw pullers, slide hammer pullers, clamp pullers, and bearing pullers. Each type is designed to handle different applications and has its own unique features. Claw pullers are the most versatile hydraulic pullers and have a wide range of applications. They have adjustable jaws that can clamp a variety of objects and are ideal for pulling gears, bearings, pulleys, and other components. Slide hammer pullers use sliding weights to generate force and remove stubborn parts such as shafts or ball joints. Gripping pullers are similar to claw pullers but have two sets of jaws that can grab opposite sides of an object at the same time. This design makes them ideal for removing items like gears or bearings from tight spaces where standard pliers-style hydraulic pullers don’t have enough clearance. Lastly, bearing pullers are specifically designed to remove bearings from shafts or housings without damaging any components. They come in two-jaw and three-jaw designs with different locking mechanisms depending on the application. By understanding the strengths and weaknesses of each type in relation to your specific needs, you can choose the right hydraulic power unit for your project. Factors to Consider When Choosing the Right Puller When choosing a hydraulic puller, there are a variety of factors to keep in mind. One of the main considerations is the size and shape of the component that needs to be removed. Since hydraulic pullers come in different sizes and capacities, it’s imperative to determine the right product for your specific application. Another factor that shouldn’t be overlooked is the type of fittings you’ll need for your job. Different types of fittings can affect how easily or efficiently you can remove a part. For example, a threaded fitting may require more force than a flat surface, which can ultimately affect your choice of hydraulic puller. When choosing a reliable hydraulic puller, you’ll also want to consider its durability and quality. A well-made hydraulic puller can last for years if properly maintained, while a poorly designed one may break down after just a few uses. It pays to invest in quality equipment as it will save you money and frustration over time by reducing downtime and maintenance costs. Safety and Maintenance Tips Safety and maintenance tips are crucial when choosing a reliable hydraulic puller. It is important to follow proper maintenance procedures to ensure the safety of the operator and the longevity of the tool. Proper maintenance includes regular cleaning, lubrication, inspection for damage or wear, and replacement of any damaged or worn parts. In addition to maintenance, it is also important to follow safety procedures when using a hydraulic puller. Operators should always read and understand the manufacturer's instructions and warning labels before use. They should also wear appropriate personal protective equipment such as goggles and gloves. When operating a hydraulic puller, users must not exceed its maximum capacity or use it for purposes other than its intended. Overall, by properly maintaining your hydraulic puller and following safety guidelines when using it, you can ensure its reliability and longevity while keeping yourself safe from injury. Cost Considerations When choosing a reliable hydraulic puller, cost must be considered. Hydraulic pullers range in price depending on their size and capacity, as well as the features they offer. Before making a purchase, it’s important to determine your needs and budget. One cost consideration to keep in mind is the initial purchase price of the hydraulic puller. While some models may seem more affordable, they may not offer all the necessary features to meet your specific job requirements. On the other hand, investing in a higher-end model with additional features can reduce downtime and increase productivity, saving you money in the long run. Additionally, maintenance costs should also be factored into your decision-making process. It’s important to choose a hydraulic puller that requires minimal maintenance and has easily accessible and affordable replacement parts. Proper maintenance can extend the life of the equipment and ultimately save you money. Conclusion In conclusion, making an informed decision when choosing a reliable hydraulic puller is essential to ensuring that the tool you invest in will effectively meet your needs. Conducting in-depth research on the different types of hydraulic pullers available on the market and their respective features is the first step in making an informed decision. It’s also important to consider factors such as the size and weight of the hydraulic puller, durability, ease of use, maintenance requirements, and safety features. Reading reviews from other users who have purchased and used the same model can provide valuable insights into its performance and reliability. Ultimately, taking the time to gather information and carefully evaluate your options will help you select a high-quality hydraulic puller that meets your specific needs. Remember to prioritize quality over cost, as investing in a reliable tool will save you time and money in the long run.